Study on Hybrid Position/Force Teaching and Control Method for 6 DoF Manipulator Utilizing f-PAWTED
- DOI
- 10.2991/jrnal.k.201215.002How to use a DOI?
- Keywords
- Direct teaching method; hybrid position/force control; teaching pendant; robot manipulator
- Abstract
In this study, a parallel wire-type teaching device with a force sensor and a hybrid position/force teaching and control method are developed to facilely teach robot manipulators using human hands instead of teaching pendants. A direct teaching method based on a hybrid position/force control is proposed to teach robots the desired position and force trajectories. The effectiveness of the developed device and method in teaching the robot manipulator is confirmed experimentally.
- Copyright
- © 2020 The Authors. Published by Atlantis Press B.V.
- Open Access
- This is an open access article distributed under the CC BY-NC 4.0 license (http://creativecommons.org/licenses/by-nc/4.0/).
1. INTRODUCTION
Robot teaching technology is essential for adequately exploiting robots. A teaching pendant has been widely utilized in the manufacturing industry for this purpose. Several teaching methods have been proposed by extant studies [1,2]. A direct teaching method using impedance control was proposed to teach robots the desired trajectories while directly moving an end effector [3]. However, this method consumes a significant amount of time, and the response of the robot during operation is poor. Hence, a Parallel Wire-type Teaching Device (PAWTED) and a direct teaching position control method were proposed [4]. An operator can handle a PAWTED to teach a Six-Degree-of-Freedom (6-DoF) robot any arbitrary three-dimensional trajectories within the working space in a short period. Subsequently, the robot can reproduce the teaching position trajectories precisely [5]. Nonetheless, the developed PAWTED cannot teach and playback both the desired position and force trajectories simultaneously.
In this study, a PAWTED with a Force Sensor (f-PAWTED) and a hybrid position/force teaching and control method were developed to overcome these problems. The effectiveness of the f-PAWTED and the proposed control method is verified experimentally.
2. PARALLEL WIRE-TYPE TEACHING DEVICE WITH A FORCE SENSOR
2.1. f-PAWTED Mechanism
The PAWTED comprises a moving platform, six wires, and a base. Meanwhile, the f-PAWTED comprises the PAWTED and a force sensor, as shown in Figure 1. The force sensor is fixed on the top face of the moving platform. The base comprises three holders, six rotary encoders, and six flat spiral springs fastened to the end of the robot arm. The moving platform is connected to the base by a system of six wires. Therefore, an operator can move the moving platform freely in a three-dimensional space. Figure 2 shows the teaching and playback operation using the f-PAWTED. In the teaching mode, the f-PAWTED measures the drawn length of the wires, whereas the operator moves the moving platform. It computes the position and orientation of the teaching tool based on the drawn lengths. In addition, the force for teaching data exerted by the end of the robot arm is measured by the force sensor. All teaching data are transformed to the robot’s reference frame Σ0 and saved in a computer. During the teaching mode, the robot is controlled to track and maintain the moving platform at a constant distance. In the playback mode, the moving platform is fastened to the holders and the robot reproduces the teaching trajectories.

f-PAWTED.

Operation using f-PAWTED. (a) Teaching mode. (b) Playback mode.
2.2. Theoretical Transformation
2.2.1. Teaching mode
As shown in Figure 2, ΣH and ΣR are the coordinate frames attached to the moving platform and the end of the robot arm, respectively. The teaching position/orientation vector of the teaching tool with respect to frame Σ0 is denoted by 0rt R6.
Similar to vector 0rt, the teaching force/torque vector 0Ft with respect to frame Σ0 is expressed as
2.2.2. Playback mode
In the playback mode, the moving platform is fastened to the base; therefore, ΣR = ΣH and RTH = I, 0TH = 0TR. The position and force data are saved as follows:
3. HYBRID POSITION/FORCE TEACHING CONTROL METHOD
A hybrid control method is proposed based on the principle that there are some directions in which position is controlled and other directions in which force is controlled. Upon a specific task, these directions change, but a single direction is never used to control both the position and force [6]. Our task is to teach the teaching tool position and force trajectories on a spherical surface using the robot attached to the f-PAWTED. The operator pushes the teaching tool with a force against the working surface while moving the teaching tool. Subsequently, the robot reproduces the teaching trajectories comprising the position and force. We assigned a moving constraint frame ΣC on the working surface, as shown in Figure 3. The origin OC coincides with the present point Ak. The ZC axis shows that the force-control direction is normal to the working surface. The YC axis is along the teaching trajectory on the working surface. The XC axis is assigned to be normal to ZC and YC, making ΣC a right-hand coordinate system. The XC and YC axes show position-control directions. The position of the teaching point Ak expressed in the working frame ΣW (OW − rαβ) comprises three parameters, (r, αk, βk), as shown in Figure 3 where r is the sphere radius, αk denotes the angle between YW and vector

Moving constraint frame on spherical surface.
Subsequently, the compensating control law of the force response in ZC-axis direction is expressed as
4. EXPERIMENTS
In this study, experiments were conducted to investigate the effectiveness of the proposed method on a 6-DoF robot manipulator (DENSO WAVE, VS-060) equipped with the f-PAWTED. Specifically, the task of writing an arbitrary curve on a spherical surface was performed. For this purpose, we created a drawing tool comprising a force sensor, pen holder, and pen as the teaching tool. The pen holder and force sensor were fastened to the moving platform. The pen was attached to the head of the force sensor and placed inside the pen holder without contact. The force sensor can measure the three orthogonal components of the force and the three components of the moment exerted on the pen. In the teaching mode, an operator grasps the pen holder and draws a curve on the dodge ball with a radius of 85.5 mm while pushing the pen against the surface of the ball. Subsequently, in the playback mode, the robot reproduces the teaching curve, as shown in Figure 4.

Playback motion of a robot equipped with f-PAWTED.
In the teaching mode, the operator manipulated the pen holder to teach the robot a closed curve starting from point A1 toward points A2, A3, and A4, and then returned to A1, as shown by the red curve in Figure 5. The controller saves the teaching data during movement, including both the position and force data of the teaching tool. In the playback mode, the data of the playback force exerted by the end of the robot arm on the dodge ball are transformed to frame ΣC. Based on the teaching and playback data of the force, an adjustment was performed according to Equation (6).
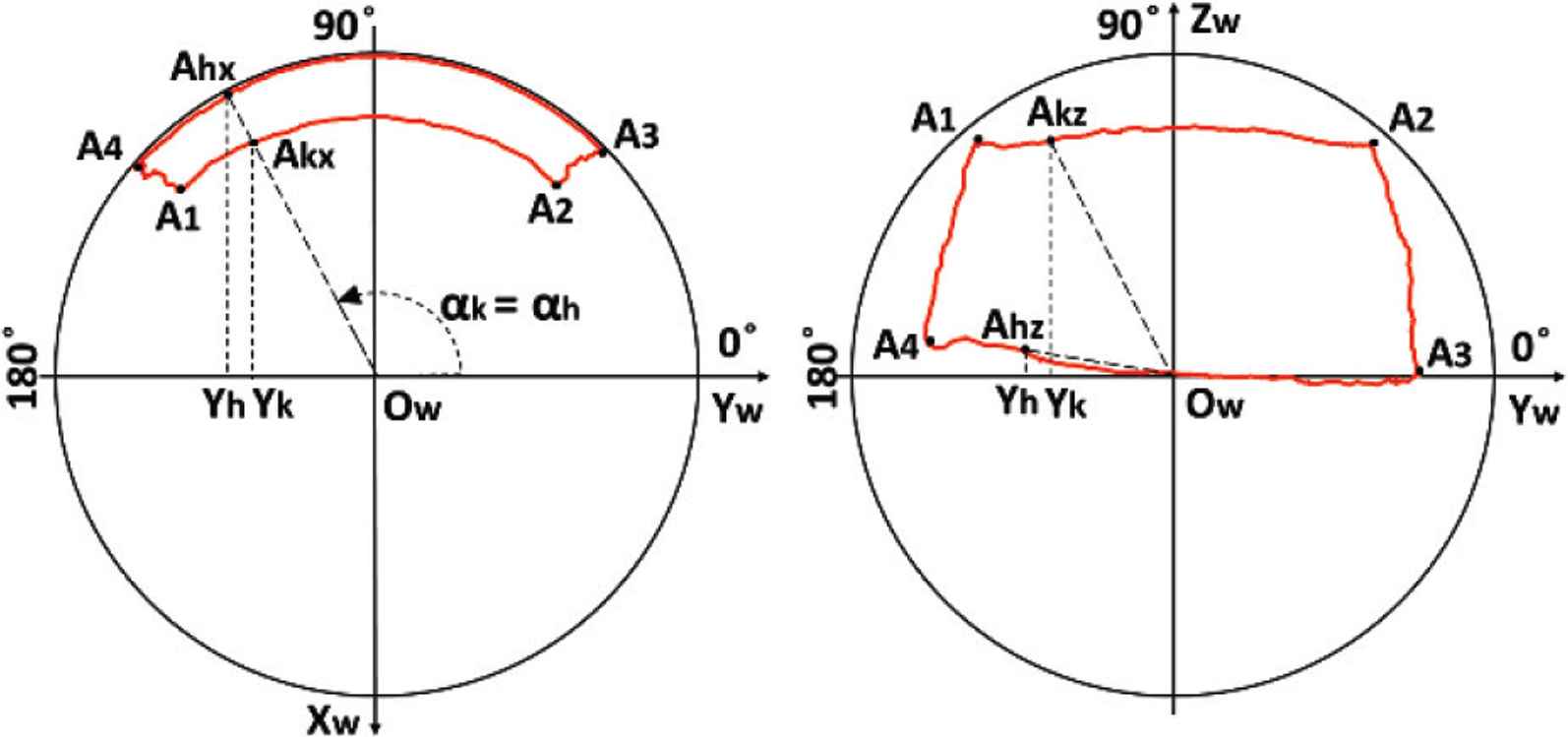
Teaching trajectory on spherical surface.
The experimental results of the force are shown in Figure 6. The horizontal axis denotes the step number of the control sequence of the robot-dedicated controller. The sampling time was 0.05–0.10 s, which depends on the movement distance of each step. The green and red lines denote the force response in the ZC-axis direction in the teaching and playback modes, respectively. The first A1 in Figure 6 represents the starting point. The next points A2, A3, A4, and A1 show the steps when the teaching tool reaches A2, A3, A4, and A1, respectively. The red line follows the green line relatively well with a mean error of 0.249 N.

Force response in ZC-axis direction during teaching and playback modes.
The position teaching trajectories with respect to frame ΣW are illustrated in Figure 7. In Figure 7, graphs (a) and (b) denote angles α and β, respectively. When the pen moved from A2 toward A3 and from A4 toward A1, angle α remained steady at approximately 45° and 135°, respectively. In addition, angle β remained stable at approximately 60° and 90° when the pen moved from A1 toward A2 and from A3 toward A4, respectively. As shown in Figure 7, the robot tracked the desired position trajectory closely. The mean errors between the teaching and playback modes of the angles α and β were 0.138° and 0.122°, respectively.

Position trajectories of teaching tool during teaching and playback modes. (a) Angle α ; (b) angle β.
Figure 8 shows the trajectories of roll, pitch, and yaw angles of orientation of the teaching tool expressed in robot’s reference frame Σ0 in both the teaching and playback modes. The playback orientation trajectories closely pursued the teaching ones. The mean errors between the two modes of the roll, pitch and yaw angles were 0.031°, 0.044° and 0.038°, respectively.

Orientation trajectories of teaching tool during teaching and playback modes. (a) Roll angle; (b) pitch angle; (c) yaw angle.
5. CONCLUSION
An approach for teaching and directly controlling both the position and force of robot manipulators using a f-PAWTED and a hybrid position/force control method were presented. The proposed method was validated by writing a closed curve on a spherical surface. Hence, this demonstrates the prospect and applicability of the hybrid position/force teaching and control method in industrial processing.
CONFLICTS OF INTEREST
The authors declare they have no conflicts of interest.
AUTHORS INTRODUCTION
Mr. Quang-Trung Chu
He received the B.S. degree in Mechatronic Engineering in 2018 from Hanoi University of Science and Technology, Vietnam. He is currently a Master’s student at the Department of Electrical and Mechanical Engineering, Nagoya Institute of Technology, Japan. His research interest is the application of robot teaching technology in the mechatronic systems.
Mr. Hiroki Tanaka
He received the B.S. degree in Electrical and Electric Engineering in 2019 from Nagoya Institute of Technology, Japan. He is currently a Master’s student at the Department of Electrical and Mechanical Engineering, Nagoya Institute of Technology, Japan. His research interest is the application of robot teaching technology in mechatronic systems.
Mr. Hideki Inuzuka
He received the B.S. degree in Electrical and Computer Engineering and the M.S. degree in Computer Science and Engineering from Nagoya Institute of Technology, Japan in 2014 and 2016, respectively. He is currently a PhD student at the Department of Electrical and Mechanical Engineering, Nagoya Institute of Technology, Japan. His current research interest includes industrial robots and teaching devices. He is a member of the JSME and IEEJ.
Dr. Yoshifumi Morita
He received the M.S. and PhD degrees in Electrical and Computer Engineering from Nagoya Institute of Technology, Japan in 1989 and 1998, respectively. He is currently a Professor at the Department of Electrical and Mechanical Engineering, Nagoya Institute of Technology. His current research interests include rehabilitation support robots, medical support systems, and robot teaching technology. He is a member of the SICE, IEEJ, RSJ, and IEEE, among other.
Dr. Masao Sakai
He received the PhD degree in Computer Science and Engineering from Nagoya Institute of Technology, Japan in 2016. He is currently a Researcher at the Aichi Center for Industry and Science Technology. His current research themes are robot teaching technology and risk assessment of robots. He is a member of the JSME, IEEJ, and RSJ.
REFERENCES
Cite this article
TY - JOUR AU - Quang-Trung Chu AU - Hiroki Tanaka AU - Hideki Inuzuka AU - Yoshifumi Morita AU - Masao Sakai PY - 2020 DA - 2020/12/31 TI - Study on Hybrid Position/Force Teaching and Control Method for 6 DoF Manipulator Utilizing f-PAWTED JO - Journal of Robotics, Networking and Artificial Life SP - 222 EP - 226 VL - 7 IS - 4 SN - 2352-6386 UR - https://doi.org/10.2991/jrnal.k.201215.002 DO - 10.2991/jrnal.k.201215.002 ID - Chu2020 ER -