X–Y Platform Synchronous Control with CANopen
- DOI
- 10.2991/jrnal.k.200221.005How to use a DOI?
- Keywords
- Controller area network; CANopen; X–Y platform; synchronous control; cross-coupling control
- Abstract
An X–Y platform synchronous control with CANopen is proposed in this paper, and the platform includes a three-phase stepping motor, motor controller and driver. The Controller Area Network (CAN) Bus is adopted for communication, and the CANopen protocol is also implemented for control. Moreover, both CiA301 standard for communication and CiA402 standard for motor control are support. The interpolation mode in CiA402 is used for synchronized control of the X–Y platform, however, Cross-Coupling Control (CCC) is proposed to improve the precision of synchronized control. The experimental results show the proposed CCC perform higher accuracy than interpolation control. The phenomenon of more position error when higher speed is also discussed.
- Copyright
- © 2020 The Authors. Published by Atlantis Press SARL.
- Open Access
- This is an open access article distributed under the CC BY-NC 4.0 license (http://creativecommons.org/licenses/by-nc/4.0/).
1. INTRODUCTION
With the vigorous development of industry, production efficiency and precision machining are more and more important. And, the high precision position control has become the main development trend of motion control. The key point of the previous discussion is detailed in this paper, such as three-phase hybrid stepping motor, Controller Area Network (CAN), X–Y platform.
Due to permanent magnet and toothed magnetic structure, the drivers of stepping motors could be triggered by pulses only. The open loop system could be performed easily for lower-accurate position control but keep constant torque [1]. However, to increase the accuracy, an encoder is installed and close-loop control is considered for higher precision [2,3] measurement the peak of driver current and control the driver current to keep the stable torque and avoid out of step. And Space Vector Pulse Width Modulation, SVPWM, is developed for higher accuracy with the high resolution step angle. The algorithm could perform an approximate sine-wave current, and the motor will be driven more smoothly. The SVPWM is implemented in this paper to perform motor driver voltage.
CAN Bus is popular for robotic control communication, because it is a real-time, fast response and low-cost distributed communication [4]. CANopen is a communication protocol based on CAN Bus, and also is device profile specification for automation, such as CiA301 standard for communication and CiA402 standard for motor control [5]. For compatibility and control performance, CANopen is adopted for synchronized control of the X–Y platform in this paper.
About multi-motor synchronized control, most literatures proposed parallel or series control [6] indicated the position error or contour error are caused by the response and load difference between motors, if the multi-motors are controlled independently. For this issue, a parallel control with a compensator as Figure 1 was proposed in Koren [7]. The compensator would provide a synchronized adjusted error, then control accuracy would be increased obviously.

Cross-coupling architecture [7].
Parallel control and CCC will be compared in this paper. The interpolation mode defined in CiA402 will be adopted in this parallel control to reduce the synchronized error between the two independent motors. Two control methods will be detailed.
2. SYSTEM ARCHITECTURE
The hardware of the system is shown as Figure 2, the proposed system includes two three-phase hybrid stepping motor and driving blocks and three controllers. The slave controller is implemented with an Renesas Rx62T microcontroller, and the master could be a microcontroller or PC. In CCC mode, the error of the other axis motor is necessary. In this paper, a user defined object in CANopen is adopted to exchange the information between the two motors.
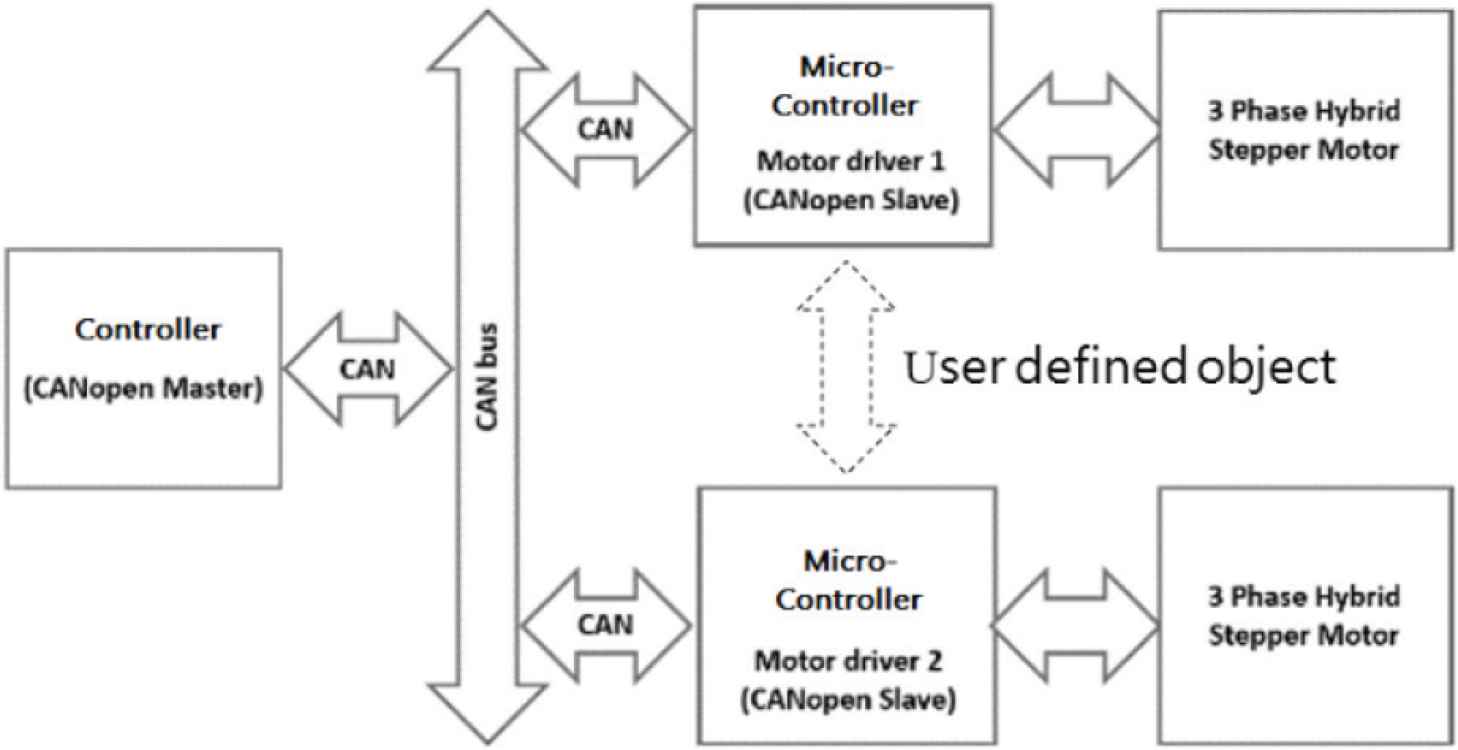
System architecture diagram.
A microcontroller, Renesas RX62T, is used to control and driver motor in this paper, and the used pins and peripherals of RX62T are shown in Figure 3. The three sets of PWM signals are used to control gate drive circuits, the required signals for three-phases six switches is generated. And, the build-in CAN peripheral is used to realize CAN communication and CANopen protocol.

Pins and peripherals of RX62T.
3. SOFTWARE DESIGN
The proposed system adopts the CANopen as the system communication. CANopen is an application layer protocol built on the CAN’s physical layer and data link layer. The basic CANopen device status and communication protocol are defined in CiA301 [4], and specification of motion control is defined in CiA402 [5]. The control methods proposed in this paper is CCC, and Interpolated Position (IP) mode defined in CiA402 is also implemented in this paper for performance analysis. Moreover, CANopen devices could communicate through process data object, which provide a fast parameters delivery between the mater and slave, or between any two slave devices.
3.1. Interpolated Position Mode
Interpolated position mode is a location control method, which is a kind of linear interpolation, as shown in Figure 4. The Xn is current position, Xn + 1 is the target, and the synchronized interval time, TSI, indicates the time difference between this two points. The interpolation time period can be set by interpolation object of CANopen, it is the time interval for next interpolated point, Xinterpolation, which is calculated from Equation (1), A first in, first out structure is implemented as the IP buffer in this paper, and is realized in the circular structure. The IP mode implemented in this paper could improve the position synchronization and increase the position accuracy for two-axis motors.

Interpolation mode.
3.2. CCC Mode
In this mode, two slave devices will exchange their position and speed information by the user defined object, then CCC will compensate the error based on two-axis errors. The tweening method is simplified to Figure 5 scheme, and the new speed and position will be calculated by cross-coupling Equations (2) and (3) [8].
Here, XN + 1 and YN + 1 the two-axis target positions respectively; EXN and EYN are the X-/Y-axis error between current and target position respectively; and Δθ is an angular displacement.

The simplified arc cross-coupling control scheme.
4. EXPERIMENTAL RESULT
The CANopen master, the RX62T board is shown in Figure 6, and the three-phase hybrid stepper motor and driver circuit board are shown in Figure 7.
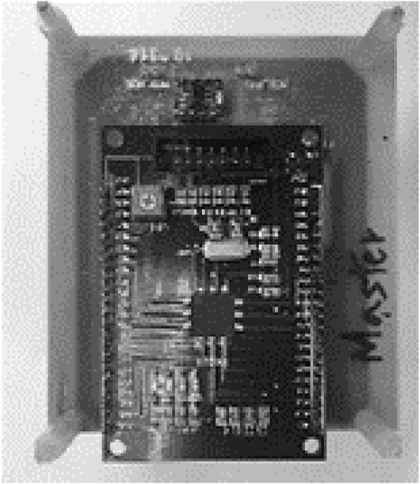
CANopen master.

Motor and driver circuit.
The experiments are set for a circular motion control with a 50-mm radius, three consecutive cycles in five different rotational speeds and two different control ways. The average Root Mean Square (RMS) of error between command and actual position is shown in Figure 8 and Table 1. The lower rotational speed, the smaller RMS error in the Interpolated Position mode and the CCC mode. The RMS errors are the almost same for all speeds under the Interpolated Position mode, however, the CCCs’ are obviously reduced when the speeds slow down.

Time for executing a circular motion in two different modes.
Time mode (s) | 79 | 94 | 125 | 188 | 376 |
IP mode (mm) | 0.0585 | 0.0569 | 0.0528 | 0.0475 | 0.0462 |
CCC mode (mm) | 0.0526 | 0.0501 | 0.0424 | 0.0356 | 0.0237 |
RMS (mm) of IP and CCC mode
To investigate the reason why RMS error increase when speed up in the proposed CCC mode, a target reached object which is defined in CiA402 to indicate the motor driver reaches the new position command or not. Because the time duration is shorted when the synchronized period is reduced, the position target may not be finished. The unreached command counts under two different control are accumulated and shown in Table 2. Note, when synchronized time <350 ms, the unreached points will increase dramatically, it means the RMS error will increase under high speed. However, if the motor runs under the system speed capability, CCC will be better than IP control.
IP Sync. time | |||||
210 ms | 260 ms | 350 ms | 500 ms | 1000 ms | |
Reached | 265 | 355 | 360 | 360 | 360 |
Unreached | 95 | 5 | 0 | 0 | 0 |
CCC Sync. time | |||||
Reached | 106 | 262 | 334 | 360 | 360 |
Unreached | 254 | 98 | 26 | 0 | 0 |
The counts of reached target at different synchronized (Sync.) time
5. CONCLUSION
A multi-axis synchronous control system based on CANopen is proposed in this paper. The standard CiA 301 and CiA 402 are also supported by the proposed system. The experimental results of circular motion show both the Interpolated Position control and CCC perform high accurate control, and the CCC mode has smaller error than Interpolated Position mode when lower rotational speed. However, the CCC provide better synchronous control accuracy under the system support speed.
CONFLICTS OF INTEREST
The authors declare they have no conflicts interest.
ACKNOWLEDGMENTS
This work is partially supported by the Ministry of Science and Technology, ROC, under contract No. MOST 107-2218-E-150-007, 107-2622-E-224-018-CC3 and 108-2218-E-150-004.
AUTHORS INTRODUCTION
Associate Prof. Chung-Wen Hung
He received the PhD degrees in Electrical Engineering from National Taiwan University in 2006. Currently, he is an associate professor in National Yunlin University of Science & Technology. His research interests include IoT, IIoT, Power Electronics, Motor Control, and AI Application.
Mr. Yu-Ming Guan
He received the B.S. degree in electrical engineering from National Yunlin University of Science and Technology, Yunlin, Taiwan in 2018. His current research interests include motor driver system and system integration.
Mr. Shih-Ting Yu
He received the M.S. degrees in electrical engineering from National Yunlin University of Science and Technology, Yunlin, Taiwan. His research interest focus on motor control.
Mr. Wen-Hua Hu
He received M.S. degree in Mechanical Engineering from University of Alabama, Tuscaloosa, USA in 1989. Currently he is an assistant professor in National Yunlin University of Science & Technology. His research interests include Iot, Digital imagine application product development and AI application.
REFERENCES
Cite this article
TY - JOUR AU - Chung-Wen Hung AU - Yu-Ming Guan AU - Shih-Ting Yu AU - Wen-Hua Hu PY - 2020 DA - 2020/02/26 TI - X–Y Platform Synchronous Control with CANopen JO - Journal of Robotics, Networking and Artificial Life SP - 254 EP - 257 VL - 6 IS - 4 SN - 2352-6386 UR - https://doi.org/10.2991/jrnal.k.200221.005 DO - 10.2991/jrnal.k.200221.005 ID - Hung2020 ER -